|
Etapa IV
Demonstrarea funcţionalităţii şi utilităţii sistemului automat pentru obţinerea piuliţelor olandeze din oţel prin extrudare indirectă la rece pe prese universale
În etapele anterioare s-au realizat: fundamentarea teoretica a gradului de influenta a parametrilor independenti, dependenti si de perturbatie specifici extrudarii otelurilor; analiza utilajelor universale, specializate si speciale pentru extrudarea la rece; modernizarea presei hidraulice PH 200 în vederea extrudarii piulitelor olandeze din otel pe sistemul automat; studiul teoretic privind stabilirea formei si calculul analitic a dimensiunilor semifabricatului pentru fabricarea produselor de tip piulita prin extrudare indirecta, la rece, din otel; determinarea analitica a volumului semifabricatului si a gradului de umplere a muchiilor piesei; elaborarea traseului tehnologic de obtinere prin extrudare indirecta la rece a piulitelor olandeze din otel; conceperea dispozitivului multipost de preextrudare, extrudare si perforare; conceperea sistemului de transfer a semifabricatelor între posturi; conceperea automatului de alimentare a dispozitivului multipost cu semifabricate; proiectarea dispozitivului de preextrudare, extrudare a piulitelor olandeze si de perforare a fundului acestora; proiectarea sistemului de transfer a semifabricatelor între posturi; proiectarea automatului de alimentare a dispozitivului multipost cu semifabricate; realizarea subansamblelor sistemului automat de extrudare.
Etapa actuala urmeaza firul logic din planul de realizare a proiectului. Astfel, s-au urmarit: realizarea experimentarilor privind obtinerea piulitelor olandeze din otelul OLC 15 pe sistemul automat de extrudare; caracterizarea curgerii otelului în procesul extrudarii indirecte la rece pe sistemul automat; analiza comportarii în exploatare a piulitelor olandeze obtinute prin extrudare la rece pe sistemul automat fata de cele obtinute prin aschiere.
În vederea materializarii obiectivelor etapei a IV-a s-a realizat ansamblul sistemului automat pentru piulite olandeze extrudate, sistem proiectat în etapa a II-a, a caror subansambluri s-au executat în etapa a III-a. Sistemul automat pentru extrudare este destinat fabricarii piulitelor olandeze M 20 cu deschiderea la cheie prin extrudare indirecta, la rece, din otel extrudabil.
Forta de extrudare este cel mai complex si important parametru, depinde de toti parametrii independenti (gradul de deformare; curba de curgere a otelului care se deformeaza; viteza de deformatie; frecarea dintre material si scule; forma si dimensiunile sculelor de lucru; dimensiunile profilului extrudat; forma si dimensiunile semifabricatului; proprietatile fizico-mecanice ale materialului semifabricatului) si determina aplicabilitatea procedeului. Valoarea fortei de extrudare este utilizata, în special, pentru stabilirea utilajului si proiectarea sculei. Pentru determinarea fortei de extrudare, în literatura exista atât relatii teoretice cât si relatii determinate experimental.
Cu toate ca exista o multitudine de relatii analitice si experimentale determinate pâna în prezent pentru calculul fortelor de extrudare, nici una nu ia si nici n-ar putea lua în considerare toti factorii de influenta, deci valorile fortelor obtinute prin relatii sunt orientative. Din aceasta cauza majoritatea cercetatorilor prefera experimentul.
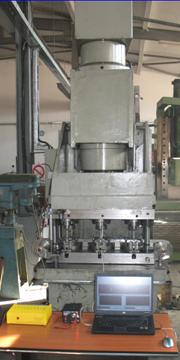
În vederea determinarii fortei la preextrudare, extrudare si perforarea fundului piulitei, precum si a deplasarii poansoanelor, în cadrul sistemului automat de extrudare, s-a utilizat un sistem de achizitie de date dinamic, format din unitatea master complet echipata, traductoare de forta si traductor de deplasare. 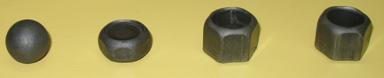
Utilizând aparatura aferenta amintita anterior s-au obtinut rezultatele experimentale preliminare privind marimea fortei de extrudare în proces. Pe presa hidraulica PH 200 s-au extrudat semifabricate de forma sferica din otelul OLC 15 tratate la suprafata prin fosfatare chimica cristalina si ungere cu grafit.
Frecarea dintre material supus extrudarii si sculele de lucru este un parametru cu o influenta foarte mare asupra rezistentei la deformare. Datorita frecarii de contact dintre material si scule valoarea rezistentei la deformare poate creste cu 30÷80%.
Determinarea valorii coeficientului de frecare m se poate face prin experiment si calcul, una din metodele avantajoase fiind aceea a refularii inelelor.
Metoda consta din încercarea prin refulare a unor inele circulare de forma cilindrica. Inelele executate din materialul prevazut pentru semifabricat, pregatite si unse corespunzator sunt supuse unor refulari axiale între doua suprafete plane si paralele. Din modificarea dimensiunilor geometrice, se pot face deductii cu privire la conditiile de frecare care au existat în timpul refularii.
Valoarea coeficientului de frecare este dependenta de modul de pregatire a suprafetelor epruvetelor. Astfel, pentru epruvete din OLC 15 STAS 880-88 pregatite prin fosfatare chimica cristalina, valoarea medie a coeficientului de frecare este fata de pentru epruvete fara tratament de suprafata.
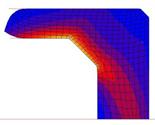
Simularea curgerii otelului prin metoda elementului finit (MEF) este necesara în scopul predeterminarii fortei totale de deformare plastica, pe baza careia se alege utilajul de deformare. De asemenea, prin simularea curgerii se urmareste determinarea tensiunilor de contact material – scule de deformare, tensiuni necesare dimensionarii sculelor, în cazul de fata a placii active, a poansonului si contrapoansonului.
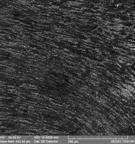
În urma studiilor de microstructura si fibraj rezultatele converg si conduc la concluzia ca odata cu marirea gradului de deformare atât pe adâncime cât si pe suprafata, curgerea metalului este îngreunata datorita unei ecruisari mai puternice. Neuniformitatea deformatiei este mai pronuntata si datorita faptului ca în cazul produselor de tip piulita gradul de deformare pe suprafata este variabil în sectiuni longitudinale apropiate. Se obtine un fibraj continuu.
Comportarea în exploatare a piulitelor olandeze obtinute prin extrudare la rece fata de cele obtinute prin aschiere se apreciaza prin tensiunile necesare ruperii fundului piulitei datorata pe de o parte fortei de strângere a piulitei în ansamblu, iar pe de alta parte presiunii de regim a fluidului transportat în instalatie.
|
|