|
Etapa III
Elaborarea modelului sistemului automat pentru obţinerea piuliţelor olandeze din oţel prin extrudare indirectă la rece pe utilaje universale
Proiectul îsi propune realizarea printr-o tehnologie avansata a piulitelor olandeze din otel, în vederea cresterii performantelor si a fiabilitatii acestora. Se aplica extrudarea indirecta la rece a otelului pe un sistem automat amplasat pe prese mecanice sau hidraulice universale, nu pe masini speciale costisitoare.
Ponderea piulitelor olandeze din otel cu mase de la ordinul zecilor de grame pâna la sute de grame este foarte mare, atât în industria constructiilor de masini si instalatii cât si în alte domenii: constructii si instalatii; industria chimica; instalatii si echipamente pentru transportul lichidelor si gazelor – conducte, pompe, supape, robineti etc.
Actualmente piulitele olandeze sunt executate prin aschiere din bara hexagonala. Aceasta tehnologie de fabricare a produselor de tip piulita este neperformanta si neeconomica datorita faptului ca necesita consumuri mari de metal, energie manopera. De asemenea, se obtin proprietati mecanice slabe datorate fibrajului întrerupt, calitate redusa a suprafetei produsului astfel procesat, productivitate mica.
Proiectul propune modernizarea tehnologiei clasice (aschiere) de obtinere a piulitelor olandeze prin aplicarea procedeului tehnologic de extrudare indirecta la rece pe sistem automat a otelului. Prin acest procedeu se elimina dezavantajele economice enuntate mai sus si se obtin produse cu proprietati mecanice îmbunatatite datorate fibrajului continuu.
În etapele anterioare s-au realizat: fundamentarea teoretica a gradului de influenta a parametrilor independenti, dependenti si de perturbatie specifici extrudarii otelurilor; analiza utilajelor universale, specializate si speciale pentru extrudarea la rece; modernizarea presei hidraulice PH 200 în vederea extrudarii piulitelor olandeze din otel pe sistemul automat; studiul teoretic privind stabilirea formei si calculul analitic a dimensiunilor semifabricatului pentru fabricarea produselor de tip piulita prin extrudare indirecta, la rece, din otel; determinarea analitica a volumului semifabricatului si a gradului de umplere a muchiilor piesei; elaborarea traseului tehnologic de obtinere prin extrudare indirecta la rece a piulitelor olandeze din otel; conceperea dispozitivului multipost de preextrudare, extrudare si perforare; conceperea sistemului de transfer a semifabricatelor între posturi; conceperea automatului de alimentare a dispozitivului multipost cu semifabricate; proiectarea dispozitivului de preextrudare, extrudare a piulitelor olandeze si de perforare a fundului acestora; proiectarea sistemului de transfer a semifabricatelor între posturi; proiectarea automatului de alimentare a dispozitivului multipost cu semifabricate.
Etapa actuala urmeaza firul logic din planul de realizare a proiectului. Astfel, s-au urmarit fundamentarea succesiunii operatiilor de preextrudare, extrudare si perforarea fundului piulitei si realizarea modelului sistemului automat pentru obtinerea piulitelor olandeze din otel prin extrudare indirecta la rece pe utilaje universale.
Pe baza desenului de executie a piesei finite, s-a elaborat desenul de piesa extrudata. Tinând seama de desenul de piesa extrudata s-au determinat elementele tehnologice necesare elaborarii procesului de extrudare la rece si anume:
- volumul semifabricatului;
- forma si dimensiunile semifabricatului;
- numarul de operatii de deformare;
Pentru determinarea volumului semifabricatului la extrudare, se aplica legea constantei volumului, deci volumul semifabricatului va fi egal cu volumul de piesa extrudata.
Pentru stabilirea formei si dimensiunilor semifabricatului s-au avut în vedere urmatoarele:
gradul de umplere a muchiilor piesei;
calculul analitic a dimensiunilor semifabricatului;
alegerea formei optime a semifabricatului.
În general, forma semifabricatului trebuie sa fie cât mai apropiata de cea a piesei finite. Produsele de tip piulita se fabrica, în general, în productia de serie mare sau masa. Este rational ca toate formele de semifabricate prezentate sa se execute, în faza productiei industriale, prin laminarea transversal-elicoidala a barelor, trecerea de la executia unei forme la alta facându-se prin schimbarea calibrelor laminorului. Pentru realizarea în faza industriala a piulitei olandeze s-a ales pentru semifabricat forma sferica. Tinând seama de legea constantei volumului s-a stabilit dimensiunea semifabricatului.
Pentru determinarea numarului de operatii de deformare , se calculeaza deformarea totala pentru întreg procesul de extrudare atât pentru înaltime cât si pentru sectiune. Din etapa I, se stie ca otelul OLC 15 îsi pastreaza integritatea pâna la un grad de deformare care reprezinta gradul admisibil de deformare plastica. Se constata ca , de unde se deduce ca deformarea se poate executa din doua operatii si anume:
preextrudare pentru ;
extrudare pentru deformarea la cota finala.
Dupa ce s-au determinat volumul, forma si dimensiunile semifabricatului initial si numarul operatiilor de extrudare propriu-zisa, se poate stabili succesiunea operatiilor, deci planul de operatii. Acesta cuprinde nu numai procesul de preextrudare si extrudare propriu-zis, dar si operatiile intermediare cum sunt tratamentele termice si tratarea suprafetei.În baza celor prezentate mai sus succesiunea operatiilor este data în continuare.
1) – tratamentul termic;
2) – tratament de suprafata - degresare, clatire, decapare, clatire, fosfatare cristalina, clatire, uscare, ungere;
3) – preextrudare;
4) – extrudare;
5) – perforarea fundului piulitei.
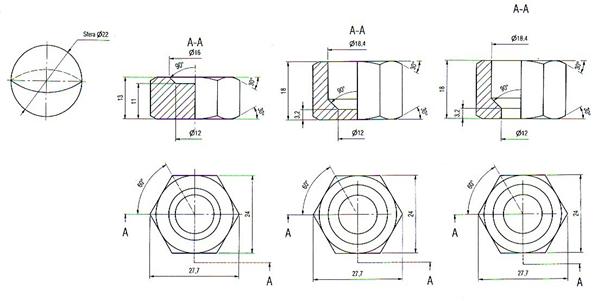
Semifabricat Preextrudare Extrudare Perforare
Succesiunea operatiilor pentru realizarea piulitei olandeze M20 (inclusiv perorarea fundului piulitei). |
În vederea materializarii obiectivelor etapei a III-a s-a realizat sistemul automat pentru piulite olandeze extrudate, sistem proiectat în etapa a II-a. Sistemul automat pentru extrudare este destinat fabricarii piulitelor olandeze M 20 cu deschiderea la cheie prin extrudare indirecta, la rece, din otel extrudabil.
Sistemul automat pentru piulite olandeze extrudate este format din trei subsisteme si anume:
- dispozitivul multipost de preextrudare, extrudare si perforare;
- sistemul de transfer a semifabricatelor între posturi;
- automatul de alimentare a dispozitivului multipost cu semifabricate.
Sistemul automat are un înalt grad de universalitate si prezinta urmatoarele avantaje:
contine trei sisteme de extractie a piesei preextrudate, extrudate respectiv perforate din locasul placii active fretate, sistem care nu limiteaza cursa partii mobile a dispozitivului; contine trei sisteme de masurare a fortei de preextrudare, extrudare respectiv perforare în vederea stabilirii rationale a presei pe care poate fi montat; se poate folosi atât pentru cercetari experimentale de laborator cât si în productia industriala; se poate utiliza pe prese universale.
Fiecare reper din cadrul ansamblului si subansamblurilor s-a executat pe baza proiectarii constructive si tehnologice a reperului respectiv, respectând breviarul: studiul desenului de executie; verificarea tehnologicitatii piesei; alegerea semifabricatului; analiza materialului; precizia de executie; probleme legate de tratamentul termic; stabilirea traseului de prelucrare mecanica prin aschiere; alegerea sculelor aschietoare; alegerea masinilor unelte; calculul adaosurilor de prelucrare si a dimensiunilor intermediare; calculul regimului de aschiere; normarea tehnica.
|
|